When we produce 316L stainless steel watches, in order to meet the needs of customers in the market, generally speaking, the case and strap need different color options. Generally, the plating colors of stainless steel watches are gold, rose gold, champagne gold, black, gun color, coffee color, and blue. Of course, there is also a white gold for those extravagant, high-end watches. Usually, this color is rarely used.
Silver is also called steel color, which is the property of stainless steel itself and does not require plating. Therefore, when we quote, the price of silver is cheaper than that of plating.
Here, I would like to speak to you about these common colors we are using ion color coating technology, then what is ion color coating?
Ion color Plating Technology
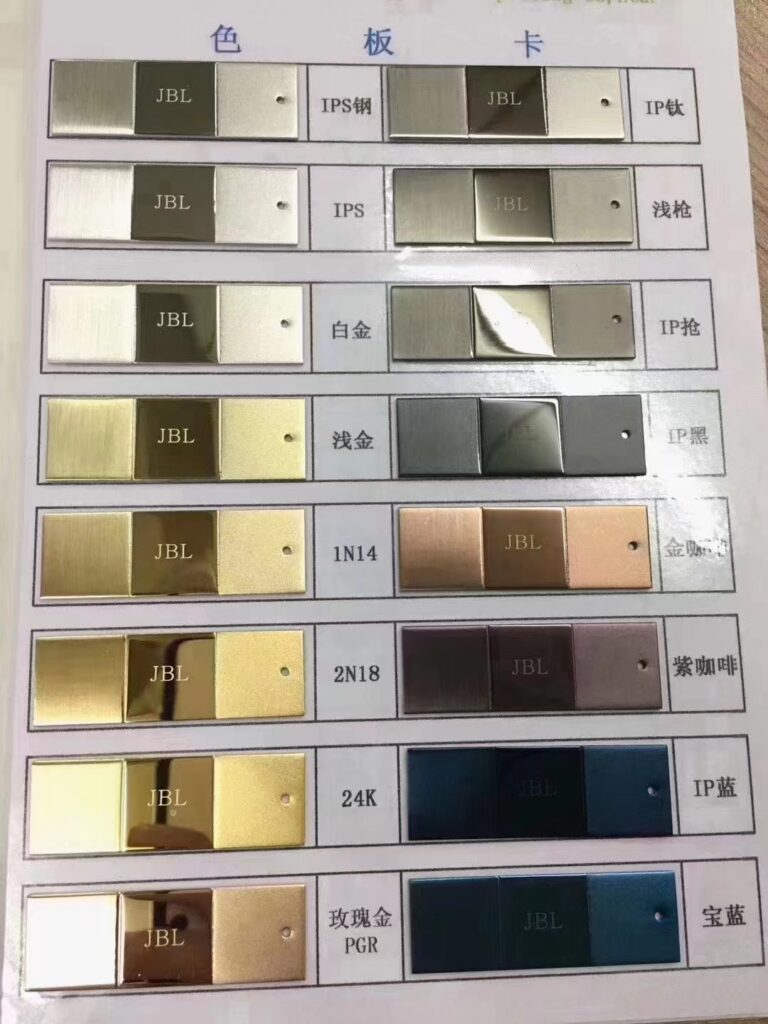

The method used for stainless steel electroplating is ion plating. The ion plating is also called PVD(Physical Vapor Deposition) plating. Ion is the chemical process where you bind tiny particles to a surface – in this case, watches. Specifically, the process bonds a small layer of metal compounds to the watch. The metals are vaporized, and in that way bound to the surface in layers, using a heated vacuum.
The common process consists: Introducing the surface to be coated in a container where the vacuum is made and adding the metals in the form of salts that are used to coat the watches. These are converted into steam using an inert gas (Argon) raising the temperature gradually. Next, an electromagnetic field is applied and the atoms are converted into ions that are attracted to the watch case surface by the charge difference. NOTE: Before the case and strap go into the container, they must be cleaned. Clean the surface of dust, and stains. Then enter the oven to dry the moisture.
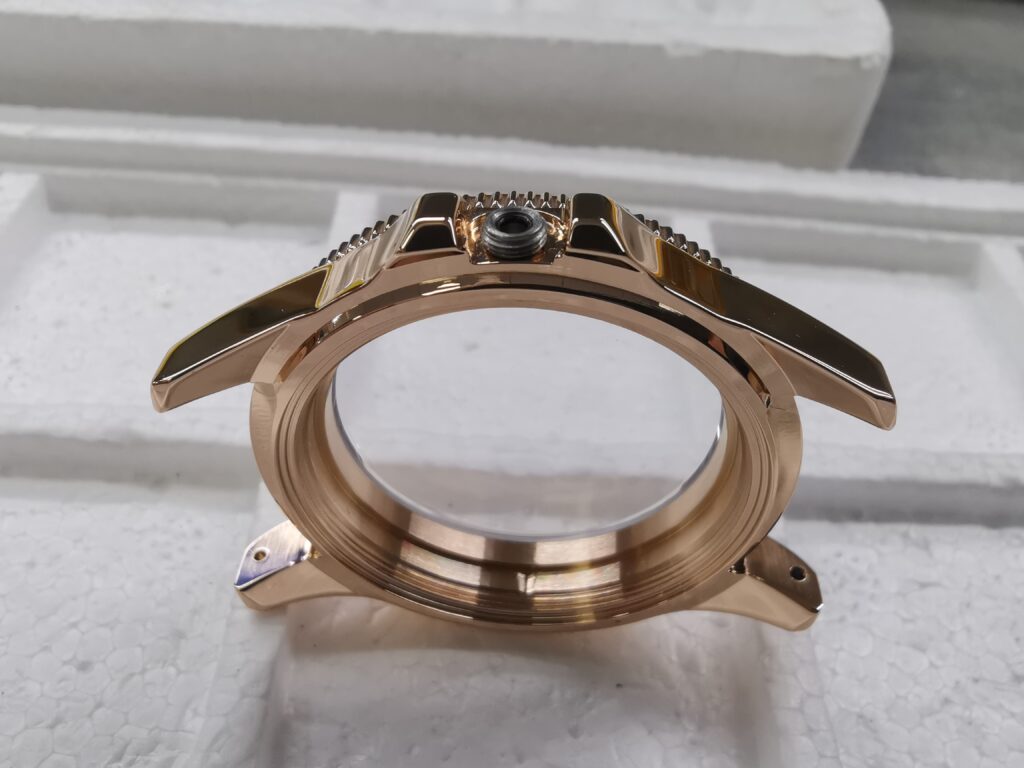
The rose gold and gunmetal color men’s stainless steel mechanical watches are the most popular in our factory.
The thickness of Ion coating
The final coating choice is determined by the demands of the application. The coating thickness ranges from 2 to 5 µm but can be as thin as a few hundred nanometers or as thick as 15 or more µm. The thickness of the watches Ops manufacture is usually 6~8 µm. Substrate materials include steels, non-ferrous metals, tungsten carbides as well as pre-plated plastics. The suitability of the substrate material for PVD coating is limited only by its stability at the deposition temperature and electrical conductivity.
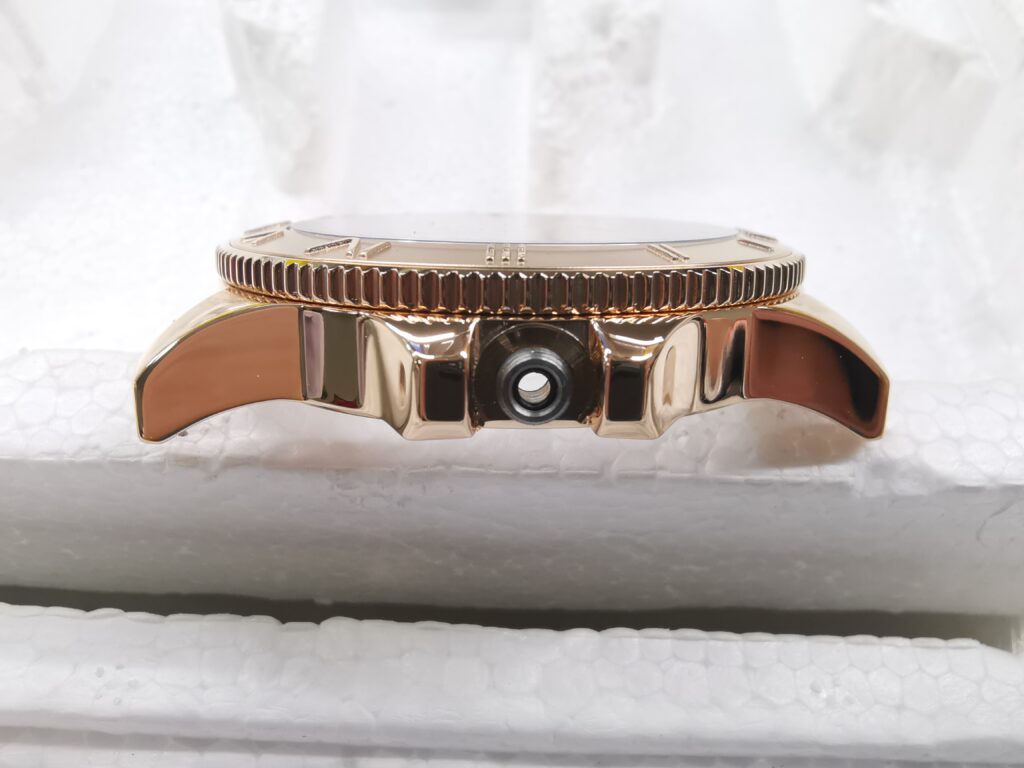